The Selection Criteria For Drilling Fluids
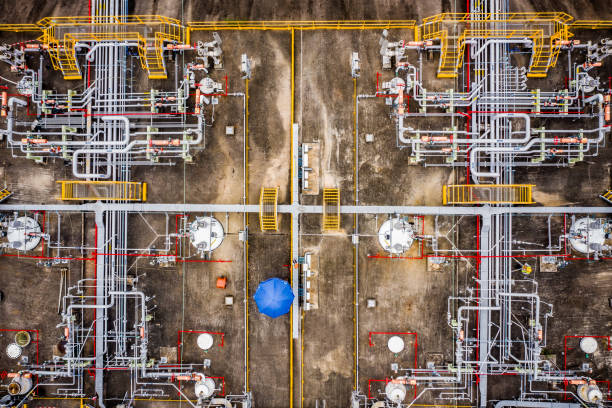
The most important criterion when designing for drilling fluid program is the
minimum cost for the overall well. Other aspects to be considered in drilling fluids chemicals suppliers
include issues related to exploration and production and environmental impacts,
performance, and logistics. The drilling fluid program is developed according to
many factors; these factors are discussed below:
Ecological Effect
When planning and implementing drilling fluid
environmental concerns are still a major consideration. In offshore operations
such as, for instance mineral oil or synthetic systems are preferable to diesel
oil-based systems.
2-Drilling can be classified into two kinds: exploratory and development
operations. When developing drilling the geological environment is well-known,
which helps to design effectively the oilfield chemical suppliers program and
optimize the other programs which are associated with it such as hydraulic
design. The information available about the area is not enough to create the
mud's properties. The mud system designed been designed to help in getting the
geological information quickly and securely. In the event of any sudden problems
or changes the mud composition should be able to adapt rapidly.
Problems related to the formation types
When drilling with bentonite through anhydritic formation, the released
calcium ions into the mud system can hinder the hydration process for bentonite,
which could affect the mud's viscosity as well as the loss of fluid. There are
two solutions to deal with the presence of ions. They can be eliminated of the
mud system by adding sodium carbonate (Na2Co3) or changing the IRO oildrilling
into an inhibitory system.
High Temperature Environment
High temperature drilling can reduce the effectiveness of chemical additives
and cause fluid loss and viscosity changes. These fluids can be resistant to
extreme temperatures and can be used in mud systems based on oil.
The formation of pressure
Fluids can get into the mud system when drilling through formations that are
high pressure. This can result in dirt contamination and unwanted kicks. To
prevent such issues it is essential to calculate the right mud weight.
Loss Flow Intervals
Drilling fluids could be lost into the formation. This problem can classified
as partial loss circulation or total loss circulation. The rate of flow from the
outlet to the hole is less than the inlet flowrate. In the second scenario, no
mud return is happening at the surface. If the fracture pressure is too high
when drilling fluids circulate or the formation naturally breaks in order to
allow mud to move through it, loss of circulation can occur.
Shale
There are many issues that can arise when drilling through shale intervals, it is possible to list them as follows:
Pipe sticking
Drag and high torque
-Hole cleansing difficulties
-Drilling liquid poisoning
Drilling Rig
The selection of the drilling fluids may be restricted by the mud control
system (solid control system and chemical treatment) and the hydraulic horse
power within the circulating system. Attaining the goals set is directly related
to the rig selection and its layout.
Casing Program
Casing setting depth is planned by a number of variables such as changes in
pore pressure trend, lithology and isolation of troublesome zones. These
requirements are also used in the design of the drilling fluid program.
Optimizing the drilling fluid program can enable drilling in deeper sections
that reduces overall cost of drilling.
Water Requirements
In the process of designing a mud program, it is important to take into
consideration the availability of drilling fluid. If the water used to make the
drilling fluid is on site, diluting is the most economical treatment. The
optimization of the solid control process will be the best choice in cases where
the water must be shipped to the rig.
Corrosion
Combining corrosion with mechanical cyclic load can cause the drilling string to break. The dissolved gases, like Co2 and H2S in drilling fluids reduce the life span of the drill pipe dramatically.
Comments
Post a Comment